خدمات بازرسی فنی جوش
بخش خدمات مهندسی جوش با تجهیزات کامل NDT
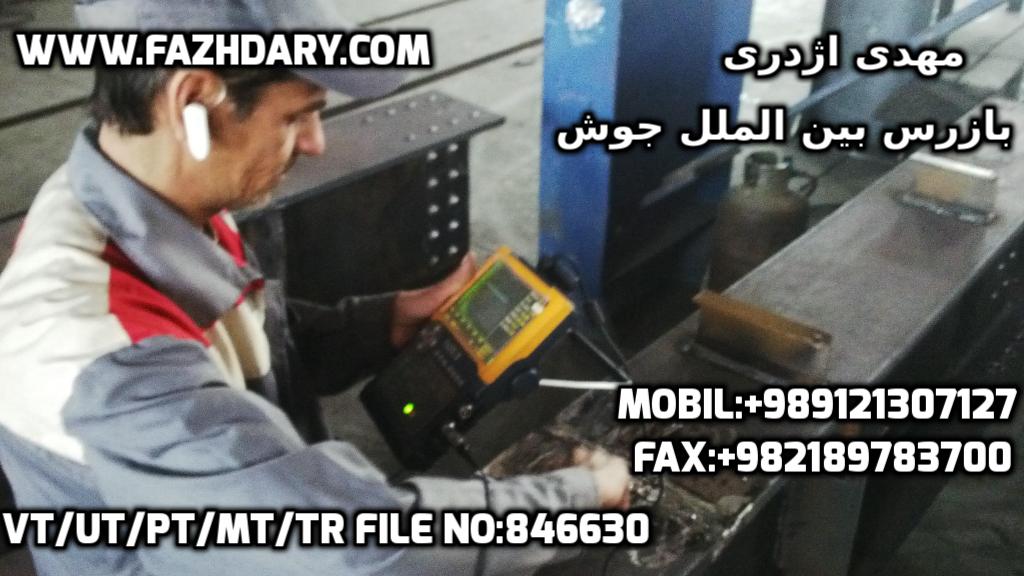
مهندسی جوش
کنترل کیفیت -تضمین کیفیت
معدن :شامل کنترل کیفیت بازرسی فنی گالری های و نقاله
سازه
کنترل و ساخت سازه فولادی در کارگاه حرفه ای مدرن و بازرسی نصب بازرسی رنگ -بازرسی ترکمت
ریل
تجهیزات بازرسی مکانیکال ریل و بازرسی جوش ترمیک ریلی
سد ونیروگاه
سد ونیروگاه: بازرسی پرتونگاری انواع حلزونی
تجهیزات پالایشگاهی
تجهیزات پالایشگاه پایپ رک -گاتر- پیچ
مخازن ذخیره نفت
تجهیزات و بازرسی مخزن تحت فشار-کروی -اندرگرند-مبدل-هیت اکچنجر-کویل-تلمبه خانه-سکوی نفتی
WPS-PQR-ITP-WQT
تولید تهیه دستورالعمل جوش کارخانه WPS&PQR
ما اینجا هستیم تا به شما خدمات مشاوره از بازدیداز کارخانه تا کنترل تجهیزات-جوشکاران و اجرای کلیه تست های غیر مخرب را انجام و گزارش تحویل دهیم
شماره تماس
- 09121307127
- email:info@fazhdary.com
- whatsapp bussiness
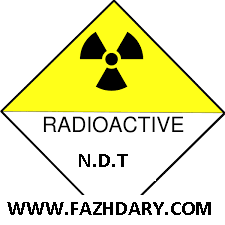
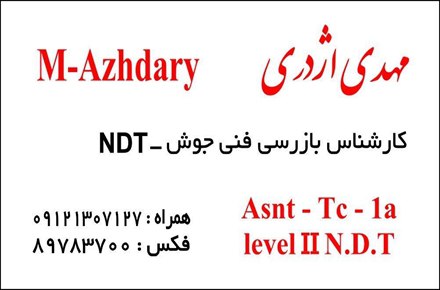
نظارت و بازرسی
- کنترل تجهیزات جوشکاری
- کالیبراسیون
بازرسی از نوع چشمی VISUALL INSPECTION TEST-VT
بازرسی بروش مافوق صوت آلتراسونیک ULTRASONIC TEST –UT
بازرسی بروش مایع نافذ LIQUID PENETRANT TEST-PT
بازرسی بروش ذرات مغناطیسی MAGNETIC PARTICLE –MT
بازرسی بروش پرتونگاري صنعتی RADIOGRPHY TEST-RT
مهدی اژدری
دارنده ایزو سطح 3 اروپا-بازرسی فنی
بخش خدمات مهندسی جوش با تجهیزات کامل NDT
Join 900+ subscribers
Stay in the loop with everything you need to know.